Designing an electric winch demands not only technical knowledge but also a nuanced understanding of the specific needs and conditions it will face. Specialists in mechanical engineering and product development emphasize that an electric winch is not merely a tool but a complex system requiring rigorous design protocols to ensure efficiency, safety, and durability.
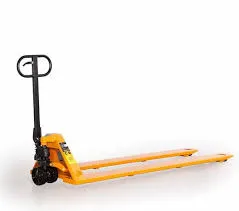
One critical aspect to focus on is the motor selection. A well-chosen motor is the powerhouse of an electric winch, determining its strength, reliability, and operating efficiency. Experience has shown that motors with a higher torque-to-weight ratio provide superior performance, especially in demanding applications such as off-road recovery or industrial lifting. Brushless DC motors are increasingly favored due to their longevity, reduced maintenance, and efficiency.
Another key element in electric winch design is the gear system. The gearing must not only magnify the motor's power but also ensure smooth operation and control. Consideration of the gear ratio is vital; a higher gear ratio delivers more power but at a reduced speed, thus it's imperative to balance between speed and torque according to the intended use. Experts recommend using planetary gear systems due to their compact size and ability to handle high torque loads efficiently.
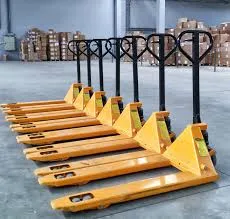
Safety mechanisms in electric winches cannot be overstated. Braking systems, both mechanical and dynamic, are fundamental. Mechanical brakes should be fail-safe and capable of holding a load securely. Dynamic braking can be incorporated to prolong motor life by absorbing kinetic energy during operation — a feature that indicates a well-designed winch respected in the industry.
The structural framework of the winch must be robust and resistant to environmental stressors. High-grade materials like aluminum or steel alloys provide the necessary strength-to-weight ratio, ensuring that the winch can endure stress without compromising on weight. Corrosion resistance is another consideration, especially for winches used in marine environments. Expert manufacturers often apply special coatings or use stainless components to enhance durability.
electric winch design
Ergonomic design and user interface are often overlooked but are vital for ensuring that the winch is user-friendly. Simple controls and intuitive layouts reduce the likelihood of operator error, thus enhancing safety and efficiency. Advanced models now incorporate smart features such as load sensors and wireless controls, providing real-time data and ease of operation. These innovations are not mere add-ons; they represent a significant advancement in winch technology, aligning with market-leading expertise.
Certification and compliance with industry standards are indispensable for establishing authority and trustworthiness. Products engineered in alignment with ISO guidelines and those bearing certifications from organizations such as CE or UL reassure consumers of their safety and quality. Compliance showcases a manufacturer's dedication to excellence and adherence to globally recognized standards.
Finally, comprehensive testing under various conditions is fundamental in the winch design process. In-field testing complements laboratory simulations by exposing the design to real-world scenarios. Gathering feedback from actual operating conditions enables designers to refine and enhance the product, ensuring it meets all performance expectations. Products that undergo such rigorous evaluation also bolster consumer trust by demonstrating a commitment to quality and reliability.
In conclusion, the design of an electric winch embodies a fusion of sophisticated engineering and practical insights, with every component meticulously optimized for performance and safety. By adhering to high standards of design, material selection, and testing, an electric winch can achieve unparalleled efficiency and reliability in any application, setting a benchmark for both expertise and authority in the industry.